Transforming the Shipbuilding Industry with Laser Cutting
The Evolution of Shipbuilding
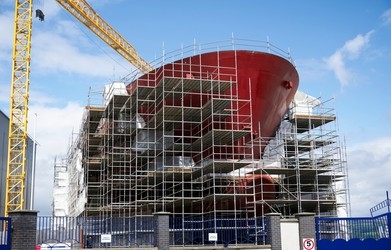
The Evolution of Shipbuilding
The global shipbuilding industry has seen great advancements thanks to laser cutting technologies. Traditional methods like flame cutting, plasma cutting, and shearing are increasingly falling short of the industry's evolving demands for precision and safety. Laser cutting technology offers a multitude of benefits, including high accuracy, safety, and the elimination of the need for secondary processing. It addresses key challenges such as slag formation, material deformation, and high operational costs.
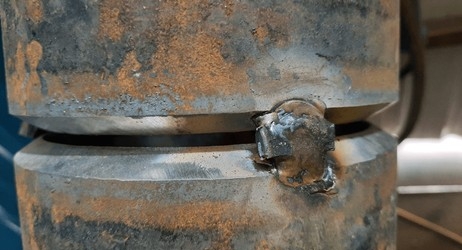
The Importance of Gradient Bevel Cutting
The industry primarily uses round pipes with diameters up to 200mm, often requiring advanced gradient bevel cutting. This technique is essential for creating intersecting line holes, oval holes, and elbows. For example, traditional fixed-angle grooves in tee welding often result in large gaps and missing arcs, complicating the assembly process. Gradient bevel cutting, on the other hand, allows for variable angle bevels based on parameters like pipe radius and intersection angle, ensuring a perfect fit and seamless splicing. This not only improves the mechanical properties of the joints but also enhances production efficiency.
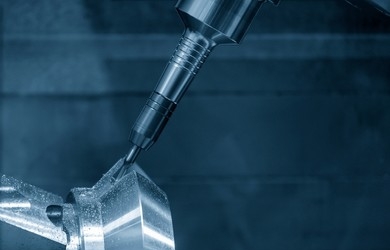
Applications and Advantages
Gradient bevel cutting is fast, burr-free, and efficient, making it ideal for various industrial sectors, including power equipment, boilers, petroleum, and chemicals. It is especially crucial for fluid pipelines and pressure vessels in the oil and gas sectors.
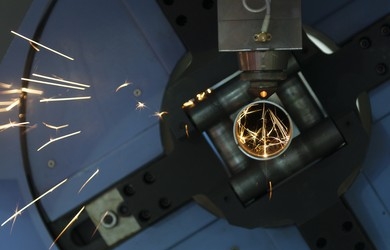
ACME Laser's Three-Dimensional Cutting Capabilities
ACME Laser offers both fixed-angle and variable-angle cutting within a ±45° range. We also provide on-demand customization for different blanking lengths, supported by a specialized blanking mechanism for intelligent feeding and picking.
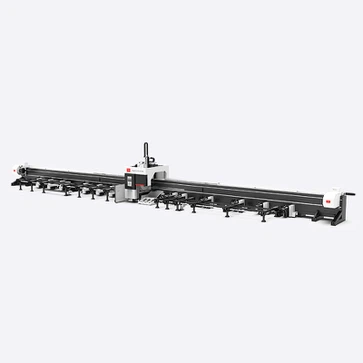