Tube Laser Machines: Elevating the Elevator $ Escalator Industry
The Growing Role of Laser Technology in Elevator & Escalator Manufacturing
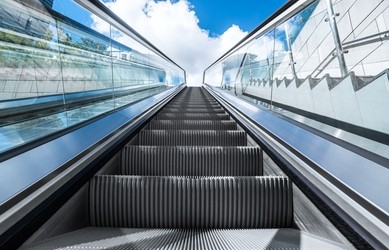
Elevator & Escalator Manufacturing
As the economy advances, so does the elevator manufacturing sector, including its accessories. The increasing demand for high-quality products has highlighted the limitations of traditional manufacturing methods. Laser technology, particularly laser pipe and sheet cutting machines, has emerged as a game-changer, offering non-contact, efficient, safe, and eco-friendly solutions.
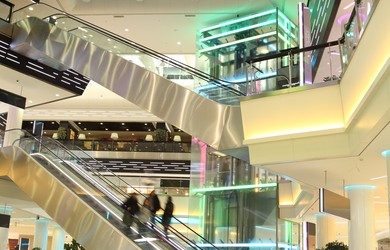
Types of Elevators Benefiting from Laser Cutting
1. Passenger and Freight Elevators: The structure and size of the profiles used vary depending on whether the elevator is designed for carrying people or goods.
2. Escalators: The weight of an escalator is determined by its structure, length, and slope, rather than simply being as heavy as possible.
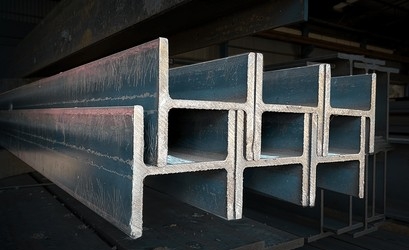
Materials Commonly Cut
Laser cutting is primarily used for the processing of round pipes, square pipes, H-steel, and angle steel. Elevator manufacturing predominantly uses 3mm stainless steel.
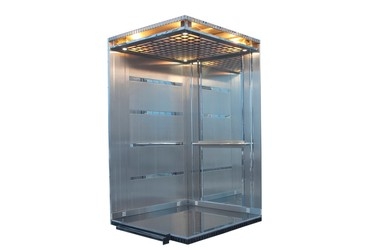
Advantages of ACME Laser Cutting in Elevator Manufacturing
Quick Turnaround: Elevator components are often customized and produced in small quantities, making laser cutting ideal for reducing development
costs.
Quality Finish: Laser cutting ensures smooth, flat lines and a high-quality
surface finish, enhancing the product's aesthetic appeal and overall quality.
Flexibility: Laser cutting can handle complex shapes and small quantities, offering a level of automation and intelligence that traditional methods can't match.
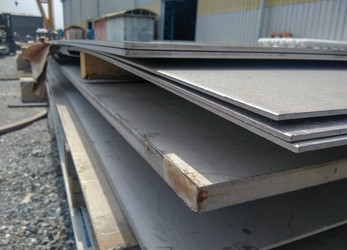
ACME's Solutions for the Elevator Industry
Traditional methods like plasma cutting and drilling machines have resulted in inconsistent quality and misaligned holes, affecting the elevator's lifespan. ACME's laser machines can process metal pipes with diameters ranging from 10-500mm and metal sheets up to 50mm thick.
