Driving Innovation Forward: Heavy Machinery Industry
Case Study: Industrial Furnaces
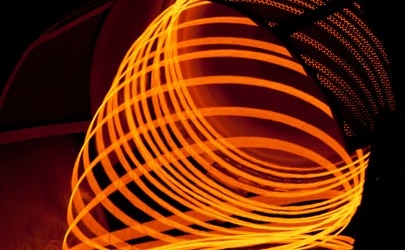
Key Advantages of Laser Processing
1. Precision in Slender Components: Laser cutting minimizes thermal deformation, ensuring high straightness in slender workpieces. Advanced
features like "micro-joining" further enhance precision.
2. Efficiency in Hole-Intensive Parts: Laser cutting eliminates the need for separate drilling processes, thereby increasing productivity. This is particularly beneficial for components with multiple holes.
3. Versatility in Cutting Irregular Shapes: Laser technology excels in cutting
complex and irregular shapes, including non-standard profiles like I-beams and channel steel, with high accuracy and efficiency.
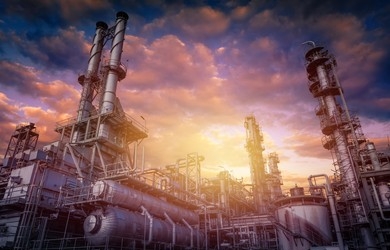
Industrial Furnaces
Industrial furnaces are crucial for various processes such as smelting, roasting, and heat treatment. They come in various types, including regenerative furnaces, trolley furnaces, and heat treatment furnaces. Acme Laser's technology is widely applicable in these areas, enhancing efficiency and precision.
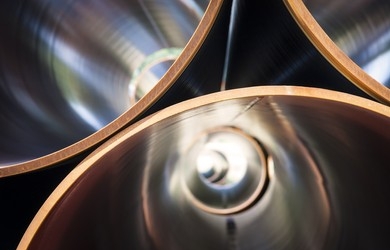
Commonly Processed Materials
Round Tubes: Mostly <350mm in size
Square Tubes: Mostly <300mm in size
Other Profiles (H, C, I): Mostly <250mm in size
Unloading Length: Up to 6 meters
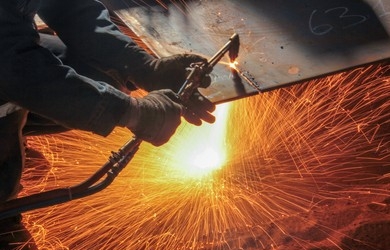
Traditional vs. Acme Laser Processing
Traditional Methods: Plasma, saw bed, and manual oxygen cutting are less
accurate, environmentally unfriendly, and labor-intensive.
Acme Laser Advantages:
o Efficiency: Eliminates manual steps, increasing production capacity.
o Precision: Allows for robotic welding due to high accuracy.
o Quality: Enhances the aesthetic appeal of the equipment.
o Cost-Effectiveness: Reduces labor costs significantly.
